H-beam Assembling Machine
1 Technical Parameter
l Suitable workpiece web height: 200-1800mm
l Suitable workpiece web thickness: 6-80 mm
l Suitable workpiece flange width: 200-1000 mm
l Suitable workpiece flange thickness: 6-80 mm
l Suitable workpiece length: 4000-15000 mm
l Single workpiece weight: < 20t
l Spot welding speed (3Hz): 360mm / min
l Machine walking speed (30Hz): 3600mm / min
l Workpiece fast conveying speed (50Hz): 6000mm / min
l Input conveyor: 2600 mm×3, Machanical operator 3 groups--One section is active
l Output conveyor: 2600 mm×3, Machanical operator 3 groups--One section is active
l Electric assemblies: Adopting AC inverter and PLC Programable Controller
l Machine power: Main frame power: 9.5KW
CO2 Welding machine rated power: 18.1 kvA×2 sets
l Power: 3 Phases, AC380V, 50Hz
2 Performance and characteristic
ZL1020 H-beam Automatic Assembling Machine is a kind of full-automatic assembly equipment for H-beam developed by ourselves based on broad market investigation and inquiry on customers. Assembling precison is better and speed is fast, maturate and steady, which have been manufactured in large batch and used in the market.
Main frame has the flange and web plate alignment and clamping function, which is driven by the interlocked unit at the same time, the flange and web alignment and clamping unit has two sets for each, which is driven by the hydraulic cylinder separately, the hydraulic cylinder pushing the rack and driven the gear transmission, the gear can driven the others transmission unit (Chain and wheel), the motion will be changed into linear traveling by the lead screw. It pushes the flange and web clamping wheel at both sides at the same time to finish the flange and web clamping and alignment. Flange and web plate adopts hydraulic cylinder pushing, not only with large strangth, but also increasing the flange and web clamping flexible. When the flange width is not equal or not regulated for cutting reason, or the thickness is variable for the web connecting welding seam, it can avoid the workpiece pass trouble automaticly.
It has the automatic hydraulic elevating baffler rack at the end of H-beam Assembling, which can ensure the alignment of H-beam web and flange. The upper press beam adopts right and left four groups of rail and asistance direction guiding, which ensures the steady when pressing. Automatic spot welding arc guiding unit is driven by the light duty oil cylinder and no need to have compress gas source. Input and output conveyor and input side has the pull rod system with segements design, the conveyor amount could be decreased or increased according to the client requirement of workpiece length. The full system adopts Japanese “MITSUBISHI” PLC to control, the main motor adopts Taiwan SANJI AC inveter speed adjusting, the hydraulic system adopts Chinese and foreign joint venture corporation standard hydraulic system product with fine colander to enasure the electromagnetism valve using long term and reliable.
Characteristic:
l The machine has a compact structure, reasonable and flexible layout: the main drive motor and reducer are placed in the middle of the lower gantry, which reduces the width of the use site; the operation box is separated from the electric control box, and the operation box can be based on the operator's operating habits And convenience is hung on either side of the main column; (not specified to be placed on the left column when leaving the factory); independent pumping stations can also be placed on either side of the main unit according to the needs of the production site. The machine shortens the longitudinal length of the main machine, allowing the operator to be closer to the spot welding position and the clamping and positioning position of the web and the wing plate, which is convenient for the operator to observe and operate.
l The equipment web and wing plates have high clamping positioning accuracy, large clamping force and wide clamping range: the clamping power is replaced by a hydraulic motor in the previous oil cylinder, which is superior to the oil cylinder in power and stroke; the mechanism consists of sprockets and chains , Screw, nut, guide seat, sliding seat, synchronous coupling and other mechanical devices; relative to the general oil cylinder directly push the workpiece, while mechanical positioning, has the advantages of high precision, stability and good rigidity. (Dental-mounted clutches are provided at the coupling part of the wing plate clamping mechanism, which can easily adjust the off-center size of the wing plate to meet the needs of special steel for the off-center web). The clamping sliding mechanism has changed the structure of the conventional sliding sleeve sliding shaft. The sliding pair in the form of a rectangular guide is used to accurately adjust the sliding gap, which can avoid the problem that the sliding sleeve protrudes too long and affects accuracy when assembling a small-sized steel profile. It also avoids the shortcomings that the component wears out and needs to be replaced after a long time in the past; the clamping mechanism on both sides is connected by a rigid coupling, the torque transmission is stable, and the synchronization performance is good; the clamping wheels at the ends are connected by eccentric shafts. The alignment accuracy can be fine-tuned (centering theoretical accuracy <1mm).
l The clamping wheel is arranged reasonably and is easy to assemble: in order to adapt to the different specifications of the assembled H-shaped steel, so that one machine can be used for many purposes and one machine is suitable; the design structure of the web clamping wheel adopts a variety of combinations. Clamping wheels are arranged in four groups at the front and rear, and the upper and lower two layers are combined, which is superior to the previous two-row two-layer and two-layer structure. It can better correct the bending of the web and improve the accuracy of alignment. According to the requirements of the thickness and width of the assembly steel plate, the best clamping cavity can be combined by disassembling the clamping wheel and changing the direction of the clamping wheel to better meet the assembly requirements and assemble a high quality H-beam. (The previous generation products cannot be disassembled and assembled, and only modified parts can be added to meet the specifications of the section steel.)
l The alignment of the section steel is accurate and the operation is simple and convenient: there is a manual alignment block at the end of the assembly machine, so that the operator can easily operate it. When the ends of the webs and wings of the H-shaped steel are to be aligned, the operator only needs to turn up the material blocking mechanism, and the ends of the webs and wings face the material blocking frame to complete the alignment work.
l Stable and flexible guiding of the lifting and lowering beam: the up and down lifting mechanism is guided by rectangular guide rails and square groove pulleys. The rectangular guide rails have the advantages of impact resistance and large force; the square groove pulleys use rolling friction, which has the advantages of low resistance and flexible rolling . During the processing, the matching accuracy of the square groove pulley and the rectangular guide rail is ensured, and the positioning performance is ensured. During the use of this mechanism, especially in the environment of steel manufacturing and processing, the wear of parts is reduced as much as possible, the maintenance cost is reduced, and the maintenance cycle is extended to ensure the reliability of long-term use.
l The automatic spot welding arc guide mechanism is scientifically designed and reasonably located: the welding torch of this mechanism is driven by a light oil cylinder, and the connection part is compressed by a live joint and a spring to ensure the stability of the pressing force of the guide wheel and the workpiece and the welding gun can follow the guide wheel to follow the center Welding seam; the position of the welding torch should be arranged under the upper pressing wheel as much as possible to ensure the accuracy of the H-beam pairing after spot welding. According to the different thickness of the wing plate, the position of the welding gun support can be flexibly adjusted up and down to meet the manufacture of workpieces of different specifications.
l The assembling speed is stable and reliable: there is an active roller table before and after the assembly machine, which is directly driven by the host motor through the chain to ensure that the linear speed of each power roller is consistent. Compared with the form of multi-motor driving, the work is more stable and the failure rate even lower.
l The equipment has a modular design and good expansion performance: the input and output roller tables and the input rod system are all designed in sections, and the number of roller tables and the number of trolley boxes can be increased or decreased according to user requirements and the length of the workpiece.
l Equipment auxiliary alignment performance is reliable, stable and convenient: an automatic hydraulic auxiliary alignment device (rod box) is installed between the input end roller table. When the workpiece is placed in the input roller table, the rod device alignment device is activated to pass through the oil cylinder By pushing the tie rod, the webs and wings can be pre-centered, and the webs can be supported without overturning; the uprights of the assembly mast are equipped with web support devices. When the webs are tall and heavy, It can effectively support the web and prevent the web from overturning, which increases the stability of the alignment and the safety of the operation.
l The equipment is simple to operate, easy to adjust, and precise to control: the main motor speed is controlled by a vector control inverter, and the vector control technology uses coordinate transformation to decompose the AC motor stator current vector into two DC components (ie, flux component and torque component) ), To achieve the purpose of separately controlling the magnetic flux and torque of the AC motor, so as to obtain the same good control effect as the DC speed control system; the speed of assembly and spot welding can be achieved by setting the inverter speed command; The assembly and spot welding time is controlled by the inverter's built-in programmable controller, which has high reliability and precise time; by adjusting the speed regulator potentiometer, the output frequency of the inverter can be changed, thereby achieving the stepless speed regulation of the roller conveyor; hydraulic The system uses standard hydraulic system products from professional manufacturers and is equipped with a fine filter to ensure long-term reliable operation of the solenoid valve.
l Operational safety: The electrical control part of the circuit uses AC 36V and DC 24V safety voltages, which can effectively protect the personal safety of the operator.
l When using automatic assembly and spot welding H-beam, the groove of the web is not less than 45°, and when the wing and web are aligned, there is no requirement to leave a gap.
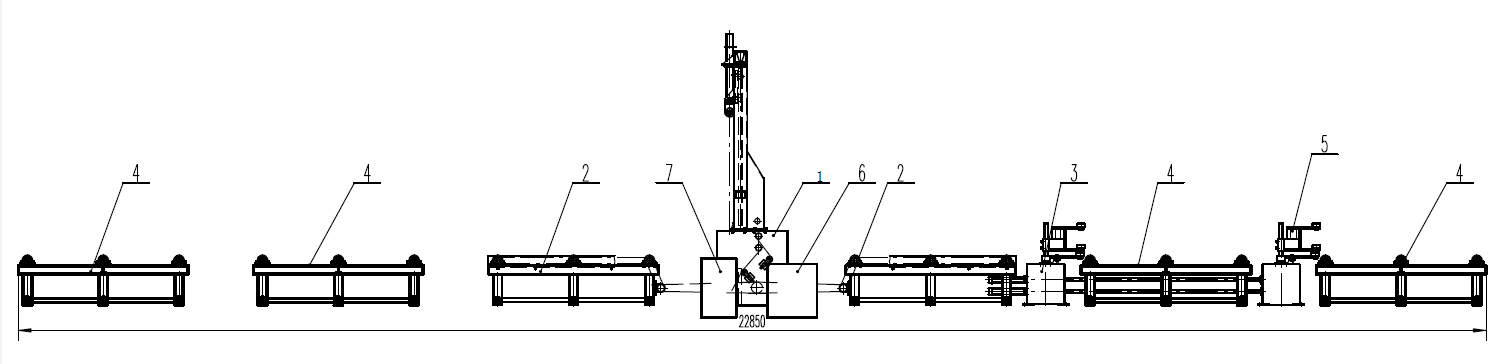
Equipment: 1-Master machine (1 Unit); 2-Active roller table(2 Sections); 3 - Take the initiative to pull rod box (1 Pcs); 4 - Passive roller (4 Sections); 5 - Driven rod box (1 Pcs); 6 - Hydraulic system; 7 - Electrical system.
3 Range of supply and consistence unit
l Assembling machine body including main frame, up gantry frame, flange and web synchronous clamping and alignment system, main transmission motor reducer, manual support device etc.
l Input roller table: 1 set (including: active and passive roller table with a total of 2.6m×3 sections, 2 sets of drawbar systems);
l Output roller table: 1 set (including: active and passive roller table total 2.6m × 3 sections);
l Hydraulic system: 1 set (including: oil pump station, high pressure hose, hydraulic cylinder);
l Electric control system: 1 set (including: electrical cabinet, control cable);
l Without welding machine, including automatic spot welding system;
l Spare parts: 1 set (including: 2 control buttons, 3 toggle switches, 2 fuse cores);
3.2.1.4 Technical document
l Machine manual operation (Includes electrical diagram and hydraulic diagram, etc.)
l Instruction manual of the inverter
l Manual of hydraulic pump station (including hydraulic schematic diagram)
l Delivery list
l A product certificate
l Drawing of machinery.
3.2.1.5 User notice
l The power line from the user's power supply point to the device is provided by the user.
l Users need to make equipment foundation and self-made parts according to the basic drawings and self-made parts drawings provided by our company. l
l When the equipment is installed, the lifting capacity is not less than 10 tons.l
l For the rest, please complete the relevant supporting requirements according to the “Preparation for Commissioning and Installation” provided by our company.
3.2.1.6 Product manufacturing acceptance specifications
The products are checked and accepted in accordance with the technical agreement signed by the buyer and the seller and the relevant contents specified in the "Q / 320206JRBF008-2008 Enterprise Standard" and "YB3301-2005 Welded H-beam" standards.
1-Upper pressure cylinder; 2-Upper beam; 3-Pillar; 4-Lifting beam; 5-Upper pressure wheel; 6-Guide arc agencies; 7-Web clamping mechanism; 8-Flange powder lock mechanism; 9-Lower beam; 10-Wall plate; 11-Main transmission roller; 12- Guide electric welding machine; 13-Motor reducer; 14-Web support device; 15-Web clamping hydraulic motor; 16-Flange powder hydraulic motor
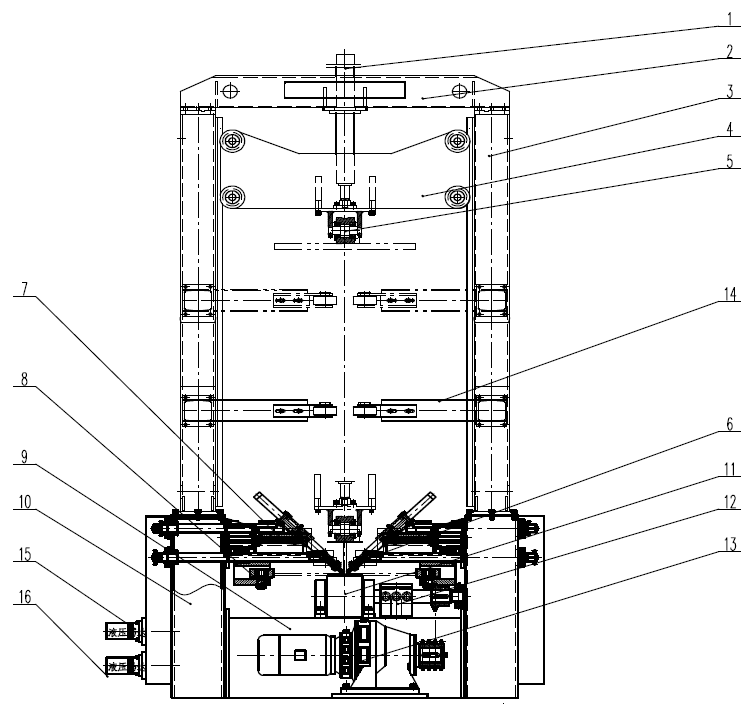